Running all through Good Manufacturing Practices guidelines is the theme of label, label, label. Label incoming materials. Label containers of raw materials. Label containers of measured ingredients when making a batch. Label bulk materials ready to be packaged. In other words, label everything as you go!
Why? Because if you rely on “remembering” what’s what, you are open to the very real possibility of forgetting what it is, how much is there, where it came from, or what it is supposed to be used for. And that’s a recipe for disaster.
Sometimes, putting labels on everything as you go along can seem like overkill. You’re probably very familiar with what the various pieces and parts of your production cycle look, smell like, and feel like, and can recognize them in an instant. If you measure out some patchouli essential oil and some peppermint essential oil, no doubt you can tell the difference instantly. So why label them?
Let me tell you a story….
Some years back I was getting ready for a big craft show. I had made a batch of each of my soaps (10 different scents) in preparation. I cut it a little too close, and didn’t have time to package all of them before I left for the show.
It was a three-day show some distance away from home. My sister loaned me her little motor home, which I was going to stay in and use as my base of operations. When I was packing up to go to the show, I gathered my unlabeled soaps in several tray boxes, along with the printed labels and packaging materials. My plan was drive down, get set up, and finish labeling the soap the night before and the morning of the show. Since I had total certainty that I could tell the different soaps apart (“The nose knows,” after all!), I didn’t take the time to put a label on the groups of soaps identifying which were which.
All was well when I arrived at the location. I got my booth set up and everything ready. Of course, after the long drive and work setting up, I was exhausted. I figured I’d get a good nights sleep and have plenty of time to finish labeling the rest of the soap in the morning, before the show opened at noon.
However, as I was soundly sleeping, the wonderful scents of my unwrapped soaps were permeating the little motor home. While it probably helped deepen my sleep, it also overwhelmed my sense of smell. By the time I woke in the morning, my smeller was completely burnt out. I couldn’t tell the difference between ANY of the soaps; everything smelled the same, including everything in the little RV!
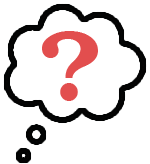
Even after opening all the windows and doors and sniffing coffee beans continually, I couldn’t tell the difference between the soaps—even my patchouli or peppermint soaps—ones that were SO obvious at any other time.
Some of the soaps I could distinguish by the color from added spices or herbs, but most of my soaps at that time were uncolored. By the time the show actually started, I had been able to label only a small percentage of the soaps I brought with me, and my sales suffered because of it.
I did remove all the soap from the RV during that first day, and between having them out of the RV and my being in the open air all day, I was able to get most of the soaps labeled that night. The second day I had enough correctly labeled soap to carry on, but I never recovered those lost sales from the first day.
Lesson learned. Always label, in some way or other, all of the pieces and parts of the production cycle. Like all the basics of good manufacturing practices guidelines, it’s a common-sense practice that will eliminate the possibility of errors in case you (or your nose) forgets.
Leave a Reply